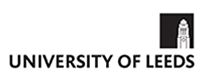
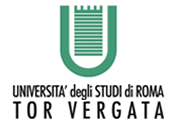
Resistance is one of the important areas that has to be taken into account in ship hull development.
An interesting possibility is to combine a CFD method and a mathematical optimization method together with a program for hull form variation. This system can then be used to find a hull form that is optimized with respect to properties computed by the CFD method, like the resistance, maximum wave height, velocity in the propeller plane, etc. One or more constraints, for instance displacement and hull main dimensions, must then be introduced to limit the modifications of the hull.
In this study by Dr. A. Pranzitelli (University of Leeds, Leeds, UK) & D. Caridi (ANSYS UK, Sheffield) demonstrating how RBF Morph can be used to achieve a 7.9% reduction in resistance for the Series 60 CB=0.6 ship hull.
TARGET:
- Optimization of the hull shape with no displacement reduction
- Reduction of the resistance
TEST CASE DESCRIPTION
Ship hull: Series 60, CB=0.6
- external hydrodynamics
- multiphase flow (air & water)
- ship advancing steadly in calm water
- trim and sinkage fixed
- displaced volume as constraint
- resistance prediction
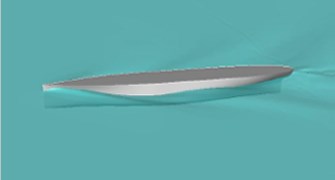
CONCLUSIONS
Performance:
- Mesh generation: 6 man-hours
- Fluent case setup: 1 man-hours
- Baseline simulation (coarse grid): 4 CPU* – hours
- Workbench and RBF-Morph setup:1 man – hours
- DOE (45 simulations): 45 CPU*- hours
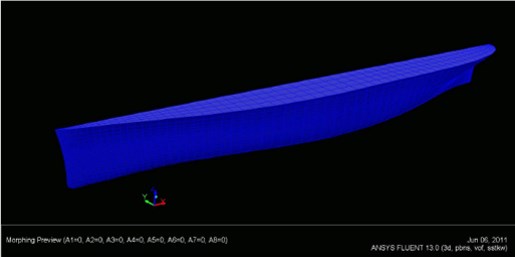
Benefits:
- integrated in the ANSYS software
- automated
- no need to go back to CAD
- no need to remesh the model
- no loss of grid quality for small deformations
- few human hours necessary
Click here for more information