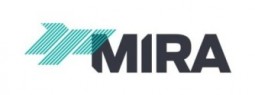
Automobile industry is facing the great challenge of energy conservation and emission reduction. It’s necessary to do some researches on some surface components of a car body to find out which of them may affect aerodynamic drag remarkably. This will help an aerodynamic engineer modify an initial car model more clearly. We also hope to reduce the cost during the process, including time and resources. The aim of the study is to develop an aerodynamic shape optimization process and achieve its automation, using a car model reference MIRA, to reduce drag while keeping a required level of downforce.
MIRA Reference Car
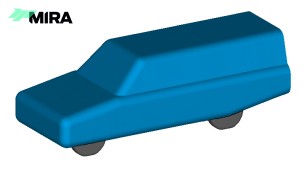
- Idealised vehicle geometry with three modular back-shapes.
- Estate-back configuration was used for this study.
The main target of the morphing/optimisation process was to reduce drag while keeping a required level of downforce (CL=-0.2).
The exterior shape of the vehicle was modified by:
- Boat-tailing of top rear back
- Changing the angle of roof
- Changing angle of rear diffuser
Shape modifiers are defined in RBF Morph
- Full Factorial DOE set-up using RBF Morph (27 design points to be fully calculated)
- Batch solution (using a single case and .rbf & .sol file of each shape, symbolic links in DOE folders)
- Post processing using a MathCAD worksheet for the evaluation of Response Surface (RS); RS is evaluated using RBF in generic n-dimensional spaces
- Optimal point detection exploring metamodel in a fine DOE (about 70000 designs explored in a few seconds!)
- New CFD run at optimal point (minimum drag with downforce constraint)
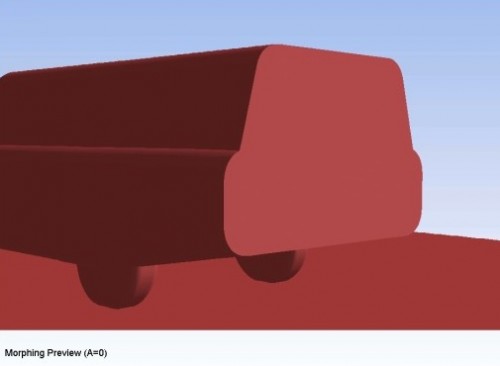
Results CP
- Optimised configuration resulted in 20% drag reduction while maintaining the required level of downforce.
Results: benefits
Significant human time reduction for the shape optimisation process:
- Standard Approach – Manual geometry modification and remeshing: estimated human time from CAD to results 5*27 = 135 hours
RBF-Morph – 1 initial case and mesh morphing: human time from CAD to results ~ 40 hours
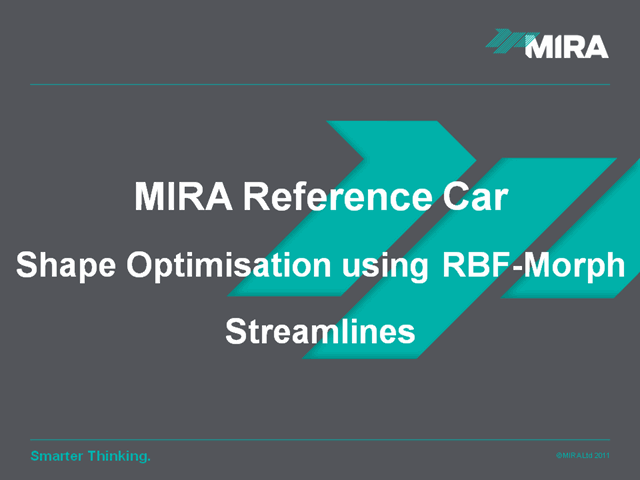
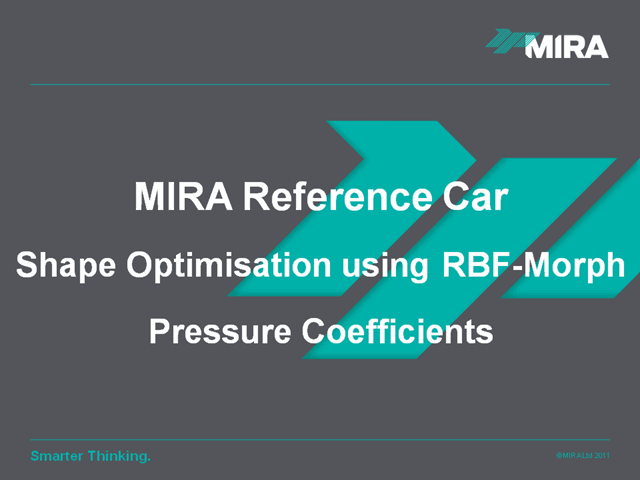
Click here for more information.